Proposed Factory for LA Relief
Warning: Array to string conversion in /var/www/wp-includes/formatting.php on line 1096
HomeLA Relief
Available factory and site with proposed overlay
LA Relief Plan
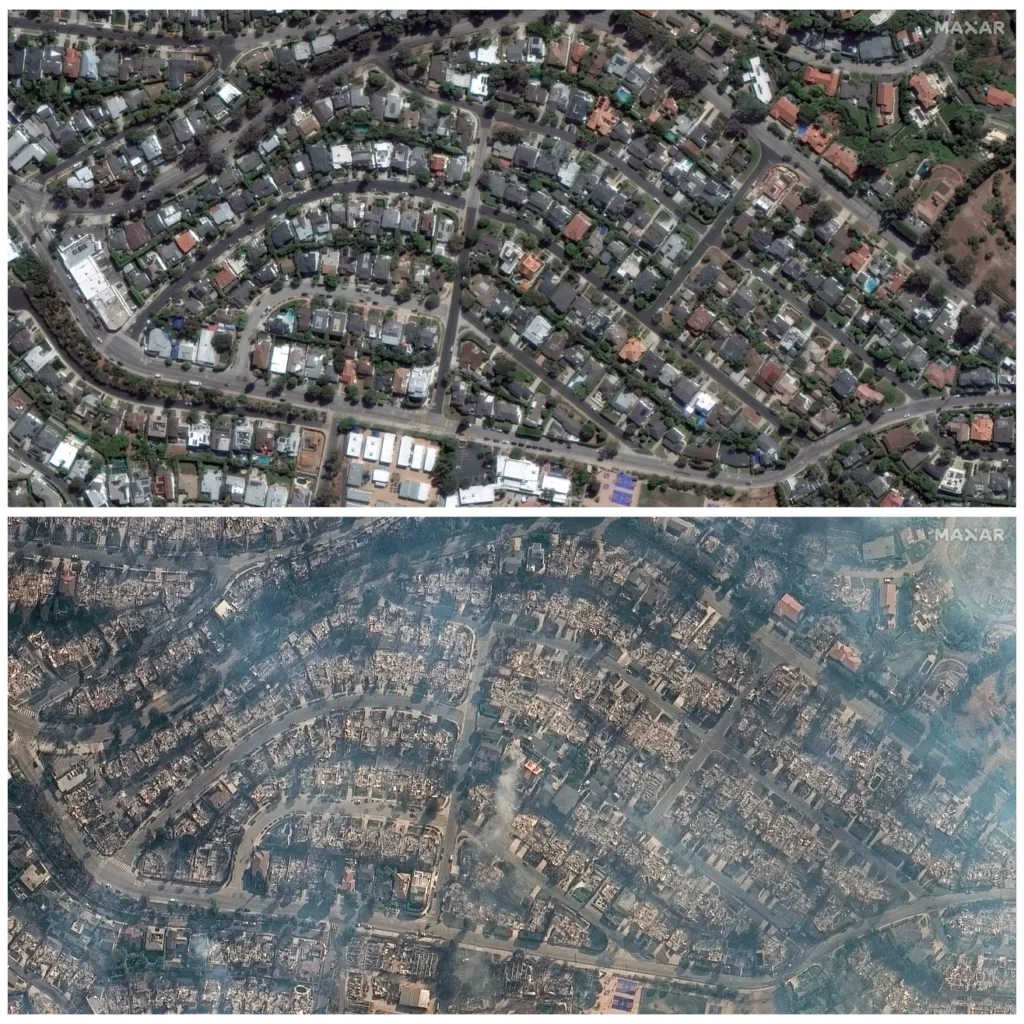
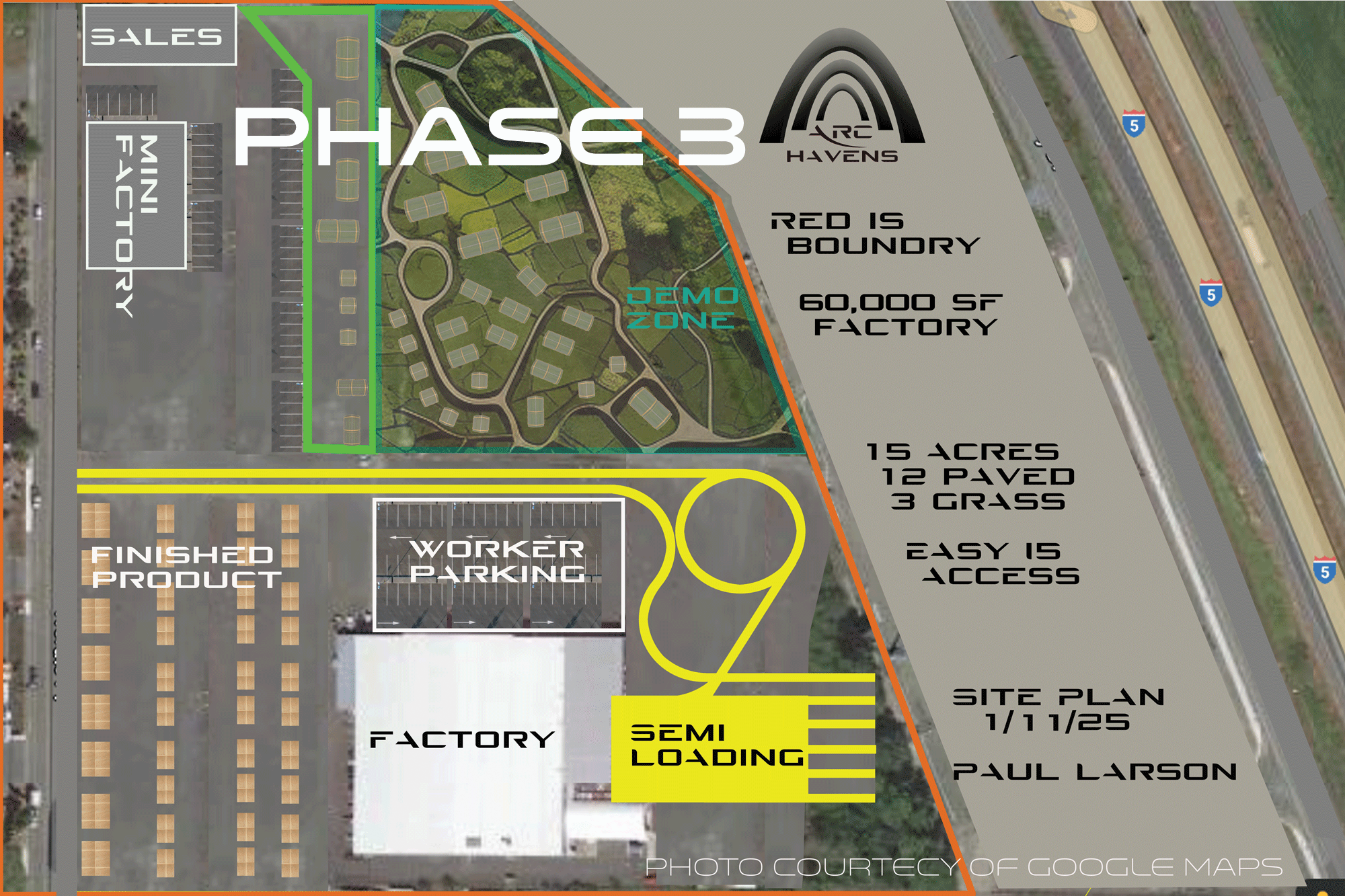
Onsite Stick built homes make no sense
After the devastating fires in Los Angeles in 2025, there is a need to supply emergency structures for the affected residents. However, the cost of stick-built homes constructed in LA is prohibitively expensive due to high building costs. To address this challenge, we propose building factory-built prefab/flatpack homes in Bellingham, WA and shipping them to LA for final assembly. This plan outlines the steps involved in implementing this solution, taking into consideration the given conditions and available resources.
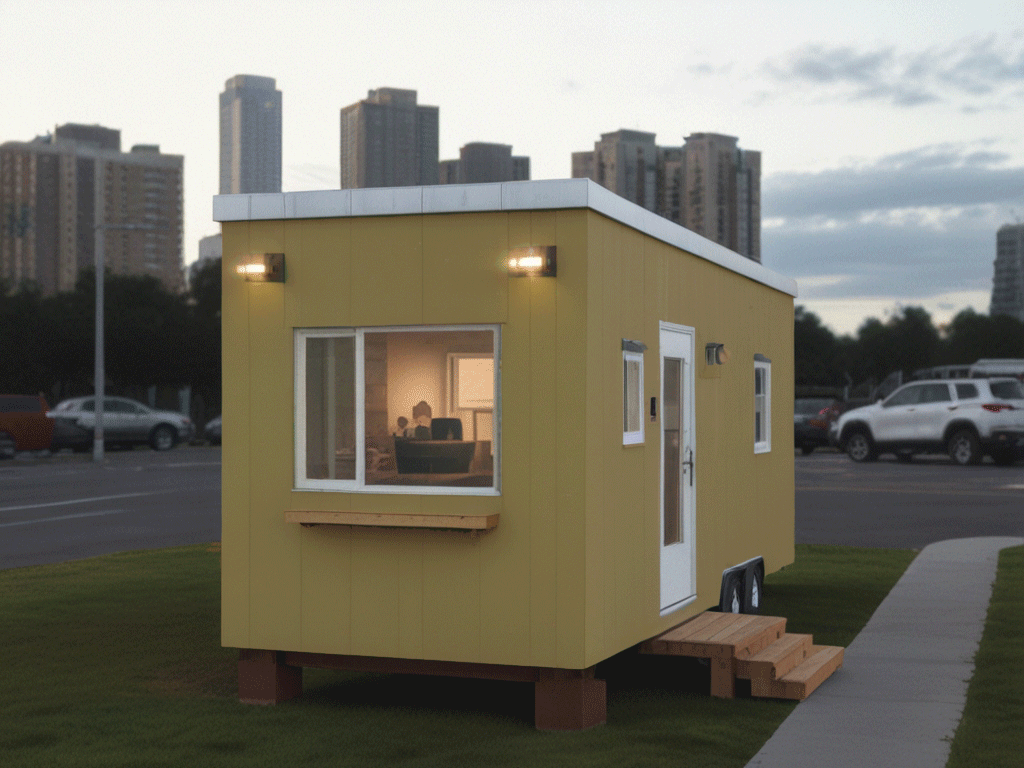
To address the urgent need for emergency and ongoing housing solutions in the wake of devastating fires in Los Angeles, we propose a strategic initiative to construct factory-built prefab modular Tiny Homes. The manufacturing process will leverage a 8,000 square foot factory available for lease in Bellingham, WA, capitalizing on the abundant Canadian lumber supply and logistics efficiencies.
These homes will be engineered to be flat-packed, optimizing them for cost-effective transportation. Lynden Shipping will facilitate the seamless delivery of these prefabricated crates from Bellingham to Los Angeles, ensuring that resources reach the affected areas promptly with regular truck shipments. For efficient distribution in Los Angeles, 53′ flatbeds can deliver directly to a designated staging area near Altadena.
Our multi-phase approach begins with Phase 1, where an 8,000 square foot empty factory will be utilized to finalize and deliver the initial units swiftly. Upon the successful implementation of these initial operations, Phase 2 will expand capabilities by integrating an additional space with a 2,500 square foot shop and a 30,000 square foot parking lot for staging packed kits and finished homes.
Phase 3 will see a substantial scale-up by leasing the abandoned Madomi prefab factory in Ferndale, WA, which includes a 60,000 square foot production facility and 1.5 acres of parking and outdoor storage. This comprehensive plan aims not only to provide immediate relief but also to establish a sustainable housing solution for LA residents affected by fires, fostering resilience and recovery in our communities.
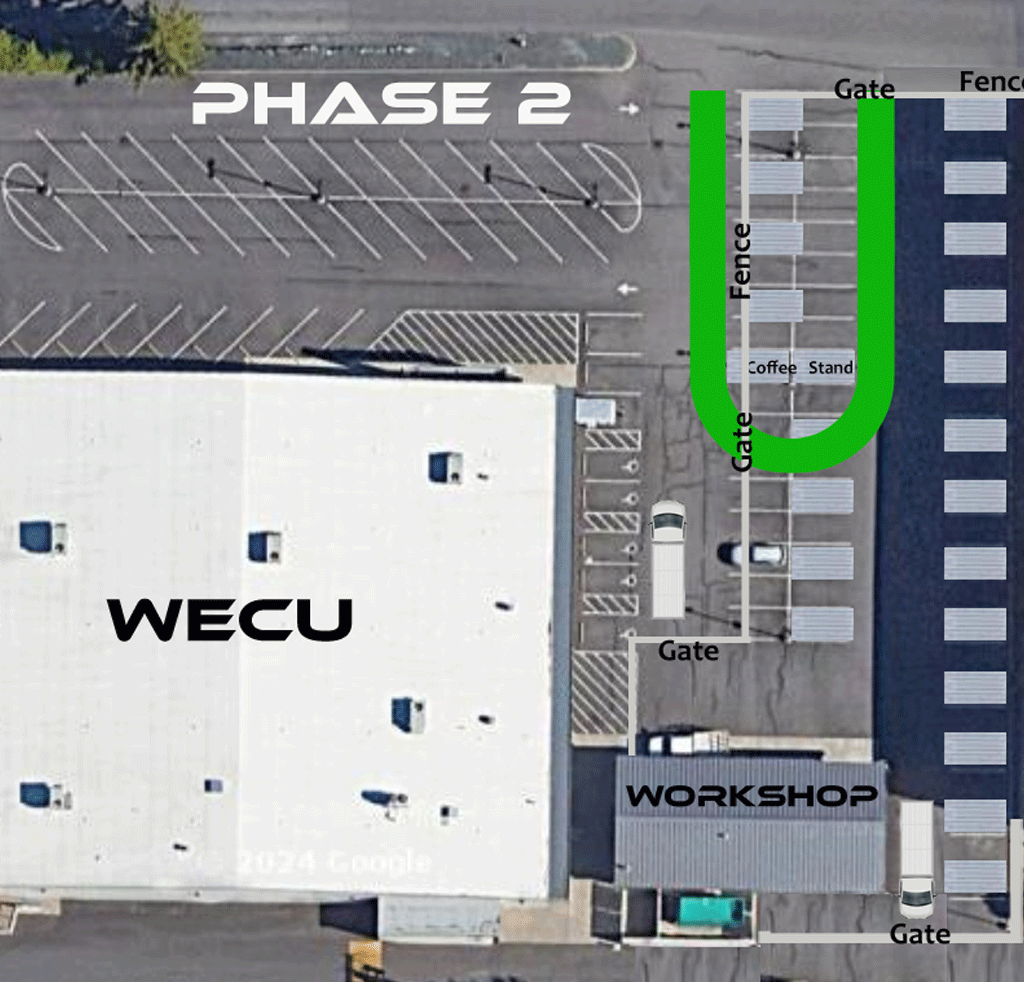
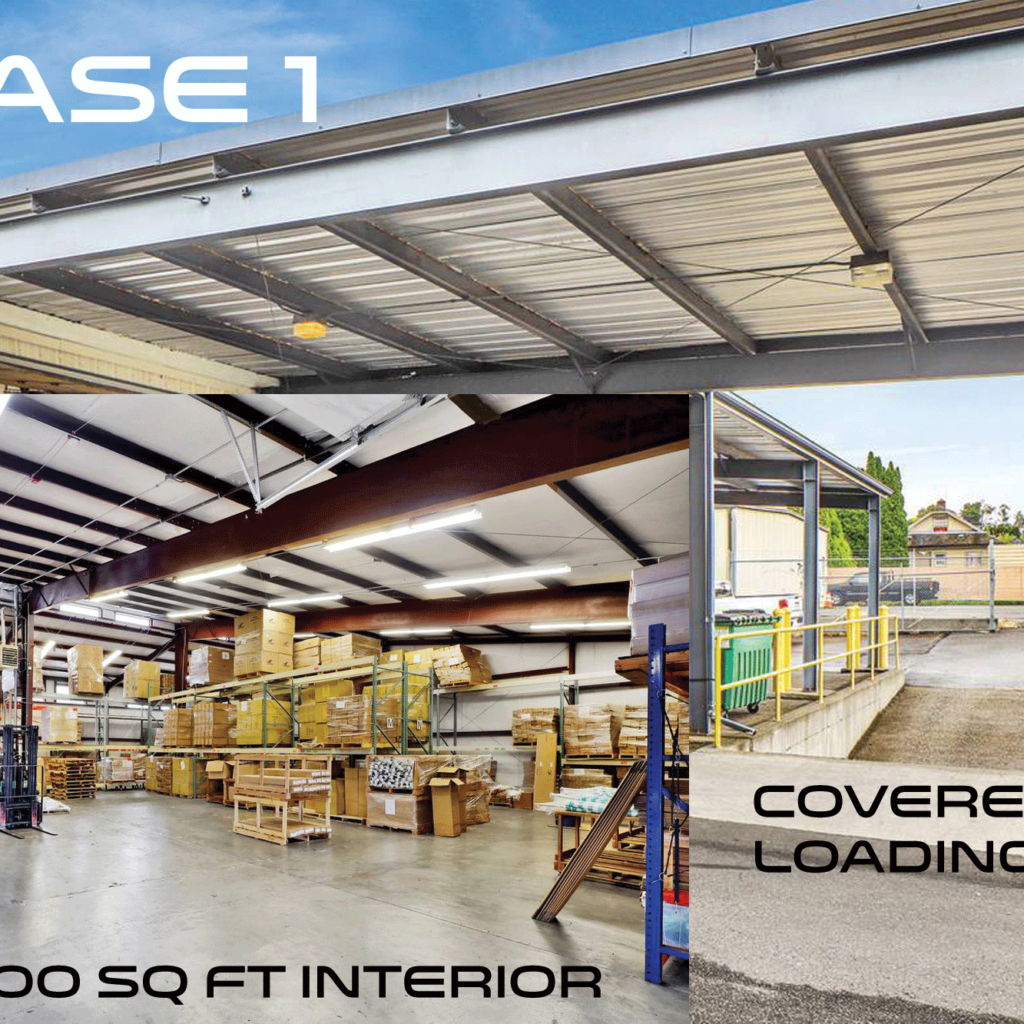
Steps for Implementing the Solution
Step 1: Design and Construction of Factory-Built Prefab Homes
1.1. Define the structure of prefab homes: Create a class called PrefabHome that represents a prefab home, with properties such as dimensions, weight, and materials used. DONE
1.2. Develop flat packing algorithm: Create an algorithm to flat pack the prefab homes efficiently into crates for shipping. Implement a function called flat_pack_homes that takes a list of PrefabHome objects as input and returns a list of crates. IN PROCESS
1.3. Calculate shipping cost: Develop a function called calculate_shipping_cost that takes a crate as input and returns the shipping cost based on its weight and dimensions. In Process
1.4. Determine optimal shipping route: Create a function called determine_optimal_route that takes a list of crates as input and returns the optimal shipping route. Done
1.5. Generate shipping schedule: Develop a function called generate_shipping_schedule that takes the optimal route as input and returns a schedule of when each crate should be shipped. Lynden shipping trucks leave Leave every Friday.
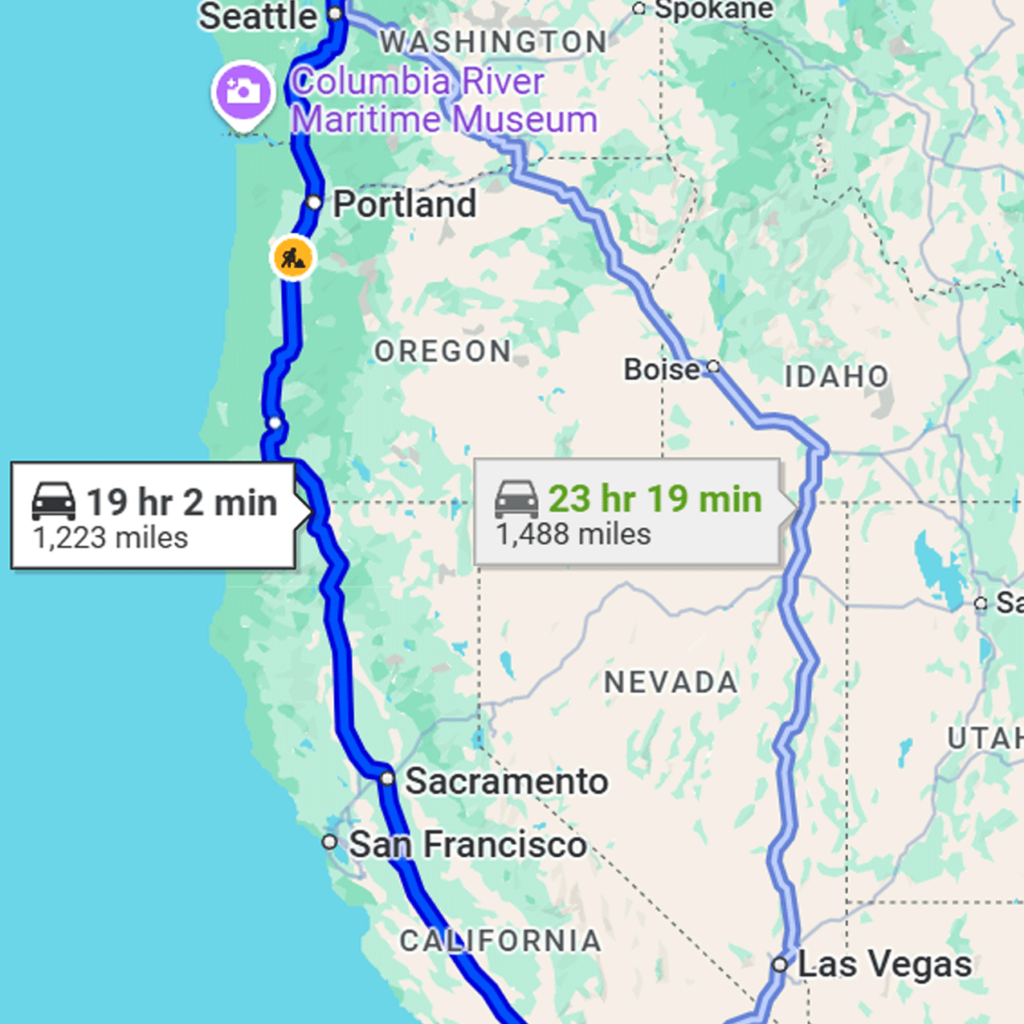
53' Flatbed
One 53′ flatbed can hold 5 15′ X 8′ units with room for assembly tools and supplies for assembly team. Subsequent shipments can hold 6 units.
Render shows one 15′ X 16′ dbl unit.
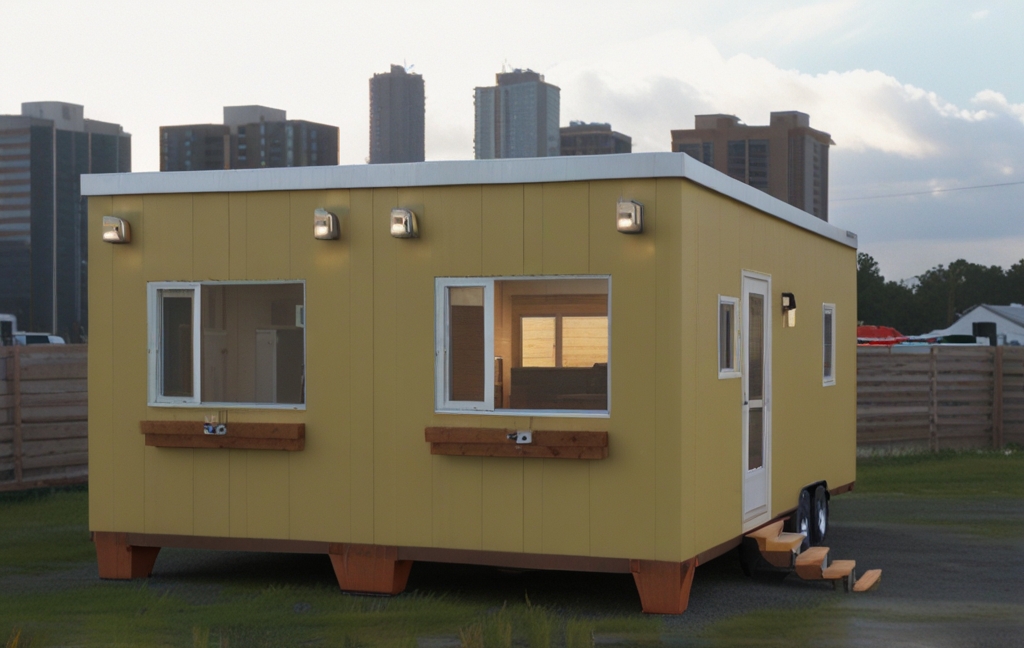
Step 2: Utilizing Available Resources
2.1. Abundant Canadian lumber in Bellingham: Source the required lumber from Bellingham to ensure a steady supply for the construction of prefab homes.
2.2. Lease the 3,000 square foot factory in Bellingham: Secure the lease of the available factory space in Ferndale to establish the manufacturing facility for prefab homes.
Step 3: Flat Packing and Shipping Logistics
3.1. Flat packing of prefab homes: Utilize the developed flat packing algorithm to efficiently pack the prefab homes into crates for transportation.
3.2. Lynden Shipping logistics: Collaborate with Lynden Shipping to transport the flat packed crates from Bellingham to Seattle using their regular truck shipments. From Seattle, utilize Lynden Shipping’s bi-monthly barge shipments to transport the crates to Honolulu.
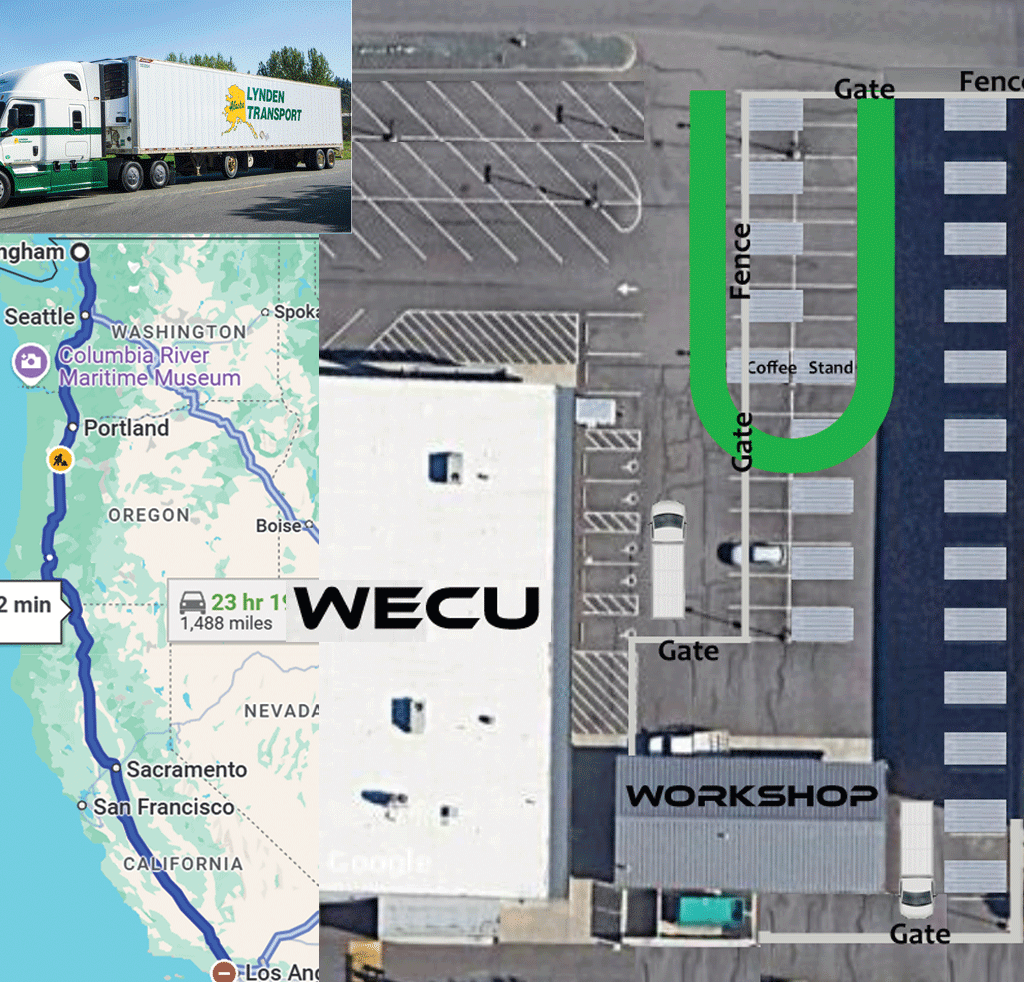
Step 4: Cost Considerations
4.1. Cost comparison: Highlight the cost advantages of factory-built prefab homes compared to stick-built homes in LA, considering the high building costs.
4.2. Cost-effective shipping: Emphasize the cost-effectiveness of flat packing the prefab homes, as purely prefab homes that cannot be flat packed are expensive to ship.
Conclusion
By implementing this plan, we can address the need for emergency housing in LA after the 2025 fires by supplying factory-built prefab homes from Bellingham, WA. Utilizing the available resources, such as Canadian lumber and the leased factories in Bellingham and Ferndale, along with efficient flat packing and shipping logistics provided by Lynden Shipping, we can overcome the challenges associated with stick-built homes in LA. This solution offers a cost-effective and timely approach to provide housing to the affected residents of Los Angeles.
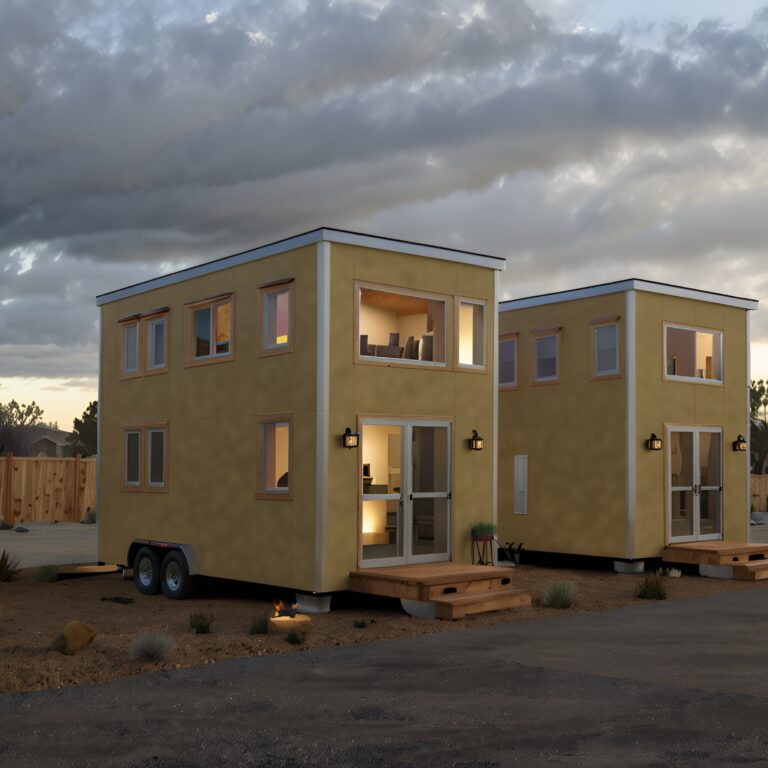